A gasket is a mechanical seal that works as filler between two mating surfaces. This helps in preventing any sort of leakage. These come in varied designs depending upon the industrial usage, physical dimensions, budget, etc.
The Spiral Wound Gasket is a mixture of metal and filler materials. The outer area of a gasket can be a circular ring or in any form made of stainless steel or carbon steel. The filler material is graphite wounded in the same way but in the opposite direction. The filler material acts as a sealing element and the metal renders structural support.
Here, the Plaint Fillers must not extend below the metal winding. The thickness of metal winding must be 0.190 mm ± 0.040 mm (0.0075 in ± 0.0015 in). It proves reliable for most of the applications and lower clamping forces as compared to the solid gasket.
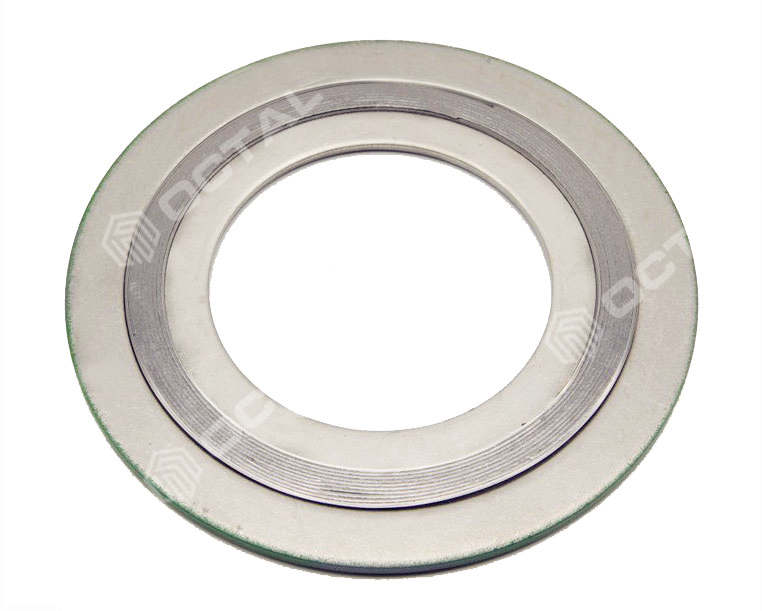
Spiral Wound Gaskets Properties
These are made by spiral winding the V-shaped metal strips and the non-metallic filler material. The metal strips hold the filler that proves gasket has mechanical elasticity and resistance. It consists of Outer Centering Ring that controls the compression, and the inner retaining ring increases the axial resilience and rigidity of the gasket. The Spiral Wound Gasket should remain in contact with the flange and must not protrude into the pipe or extend from the flange.
It includes three parts:
- Filler: Its thickness ranges from 0.5mm to 0.6mm. It contains flexible graphite 99.85%, Flexible Graphite is 98%, and Micalit, Ceramic, PTFE & EPTFE.
- Centering Ring: The Spiral Wound Gasket must be assembled and furnished into the centering ring. Its thickness shall range from 2.97 mm to 3.33 mm (0.117 in. to 0.131 in). This must be grooved on the inside of a diameter in order to retain the gasket. It does not come into direct contact of the contained fluid. This is made of carbon steel pointed or plated to avoid corrosion.
- Inner Ring: It helps in avoiding excessive compression occurring due to high-seating stress. The Inner Ring also decreases the turbulence in a flange area. It must be furnished with the Spiral Wound Gasket consisting of PTFE or Polytetrafluoroethylene filler material.
Benefits
- Easy to Install, with lower pre-loading pressure.
- The solid structure provides sealing and stability even if the sealing surface is bent or corroded.
- Under Heavy Operating Conditions, sealing is carried out.
- In case of pressure fluctuations, it renders reliable sealing performance and strong stress compensation stable.
- Compatible with a wide range of working conditions, against for high pressure, high temperature, ultralow temperature or vacuum circumstance. By using different material combination, it can solve different chemical corrosion.
Notes for Gasket Installation
When the gasket is installed on a new flange or an old one is replaced, here the flange faces must be free and clean from scoring and indentations. Here, cross-face scoring can lead to leakage.
- Before installing the gasket, check that it is not damaged and meets the requirements too.
- The faces of the flange must be concentric and parallel so that they do not need to be pulled into a position where the bolt load is quite large.
- The Spiral Wound Gasket should never be re-used and only the newer one must be used.
- The Lubricants or the Jointing compounds should not be used.
- After installation, ensure the flange faces to be parallel. It can be noticed with a flange gap measurement tool.
Applications
Spiral wound gaskets are widely used by industry in processing piping and equipment. Most of these gaskets are pipe flanges produced in accordance with ASME B-16.20 metal gaskets for pipe flange. Correctly produced and installed SWs are very reliable gaskets, and they have been successfully used in high pressure and high temperature applications.
Spiral wound gaskets are special semi-metallic gaskets of great resilience, therefore making them suitable for applications with heavy operating conditions. Spiral wound gaskets can be used for sealing flange joints, manhole and handhold covers, tube covers, boilers, pressure vessels, pumps, compressors and valves. They are also ideal for steam, oil, liquids, gases, acids, various organic mediums ans solvents.